Free Shipping on Selected Items
Lifting Equipment / LOLER Examinations
To comply with Regulation 9 of LOLER (UK) or Regulation 52 of the General Applications Regulations No. SI 299 (ROI), lifting equipment must undergo examinations (often called lifting equipment inspections or LOLER inspections) at specific intervals during its operational life
For new or moved equipment
All lifting equipment needs to be tested when it is first put into service
- When lifting equipment is put into service for the first time, a lifting equipment / LOLER examination is required. This is normally covered by the CE or UKCA and subsequent Declaration of Conformity.
- When equipment is installed or relocated and re-installed, it must undergo a lifting equipment/LOLER examination to ensure proper installation and safe operation. For instance, with a Two Post Vehicle Lift, a competent person should oversee the installation process to ensure it meets the manufacturer's specifications. Once the installation is confirmed satisfactory, a Report of Thorough Examination after Installation should be issued. This report must be retained with the equipment throughout its service life.
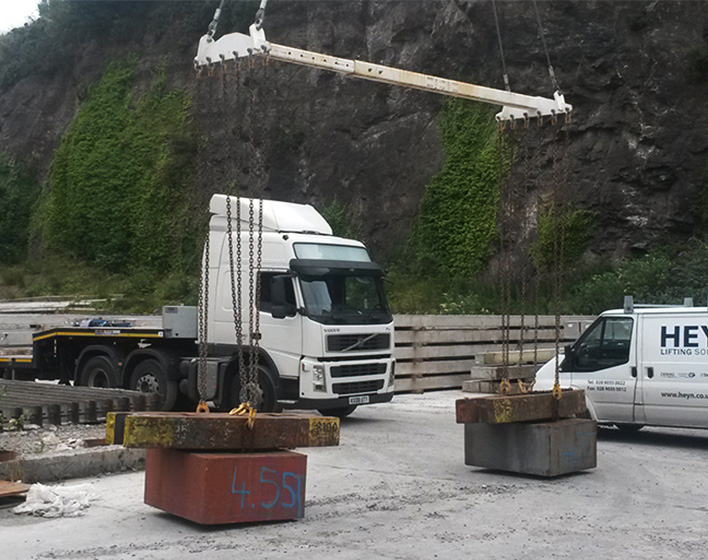
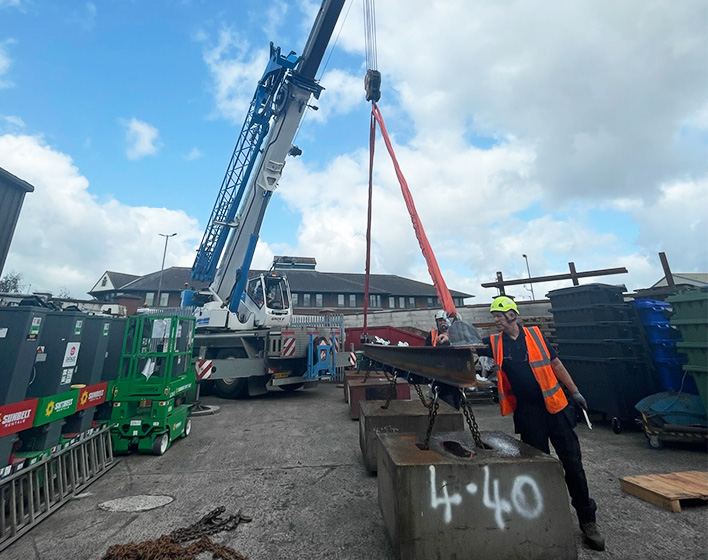
What to do if equipment has been used for a period of time?
Lifting equipment must undergo a thorough lifting equipment/LOLER examination after being in service for a certain period to ensure it has not deteriorated to a dangerous level. UK and ROI legislation specifies the intervals for these examinations as follows: Lifting accessories: every 6 months Lifting equipment: every 12 months Lifting equipment used for lifting or lowering persons: every 6 months
Ensuring Workplace Safety: The Crucial Role of Testing Lifting EquipmentWhat to do in exceptional circumstances?
A thorough lifting equipment examination is required whenever exceptional circumstances arise that could compromise the safety of the equipment. This examination is also necessary after any significant change that may affect the equipment's safe operation. Such instances include:
- Involvement in an accident or dangerous occurrence, such as overloading or component failure
- Significant changes in conditions of use, such as increased usage, changes in loading (e.g., from inert loads to chemicals), or a shift in the work environment (e.g., moving from indoor to outdoor use)
- Long periods of inactivity
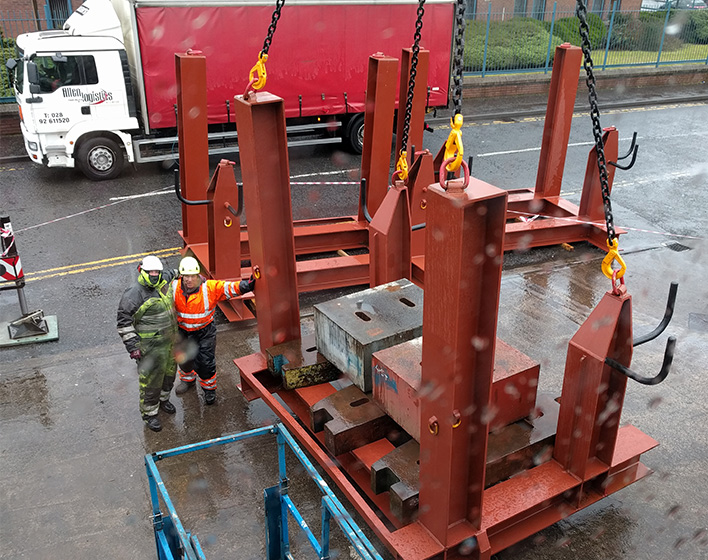
What Heyn Engineering can offer?
Located in Belfast, we have over 50 years of experience testing lifting equipment.
We have a team of field engineers who service the whole of Northern Ireland and we also have the ability to conduct bespoke tests here on site using specialised equipment.
Our most common tests include
- Jack Inspection
- Tail Lift Inspection
- Crane Inspection
- Hoist Inspection
- Loose Lifting Gear Inspection
- Vehicle Lift Inspection
- Plant and Machinery Inspection
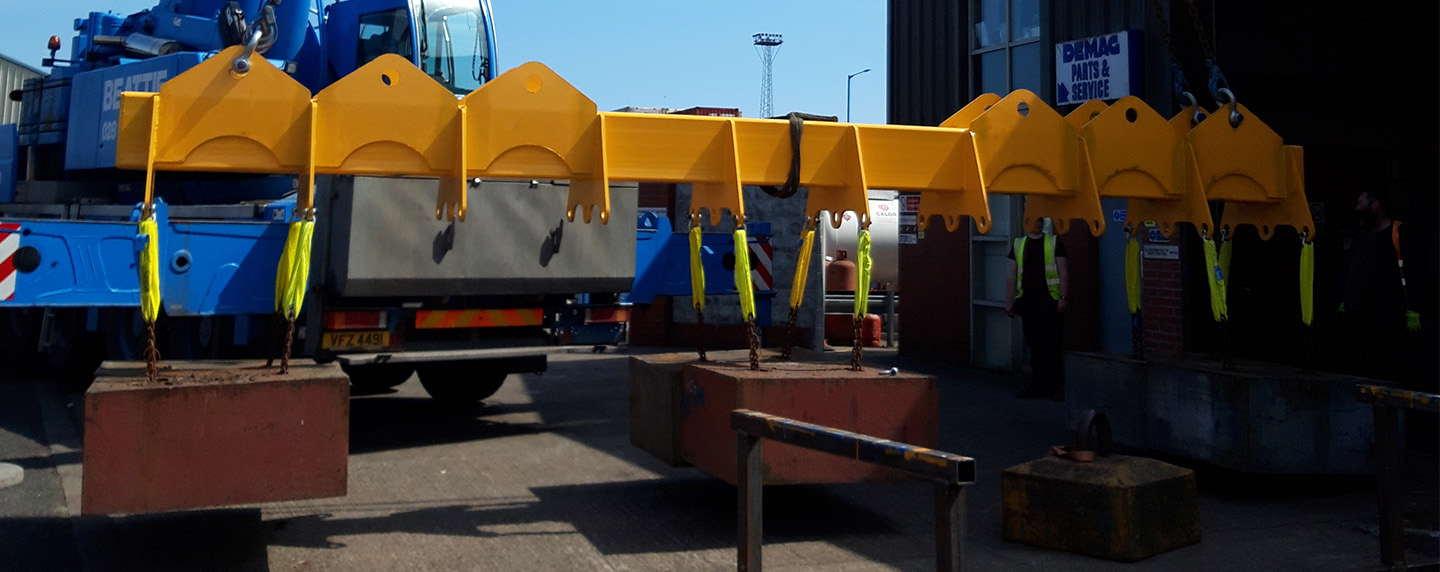